Accueil>Entre délocalisations, intensification, et digitalisation : travailler dans l’industrie automobile aujourd’hui
12.09.2024
Entre délocalisations, intensification, et digitalisation : travailler dans l’industrie automobile aujourd’hui
L'auteur
Juan Sebastian Carbonell est sociologue du travail et des relations professionnelles. Il est post-doctorant au Gerpisa, à l’Ecole Normale Supérieure Paris-Saclay, et chercheur associé à l’IDHES. Il mène des recherches sur le travail, la négociation collective et le changement technologique principalement dans l’industrie automobile française. Il est l’auteur de Le Futur du travail (Éditions Amsterdam, 2022).
La contribution
Deux images d’Épinal se font concurrence dès qu’il est question du travail dans l’industrie automobile aujourd’hui. D’un côté, celle héritées des Trente Glorieuses et de récits militants, qui décrivent un travail saccadé sur une chaîne de montage sale et bruyante. On y verrait un travail parcellisé, monotone et abrutissant. De l’autre côté, celle des discours modernisateurs, qui mettent l’accent sur les nouvelles technologies, où les robots auraient libéré les ouvriers des tâches les plus pénibles et rendu le travail plus intéressant et épanouissant. On trouverait donc dans les usines moins d’ouvriers spécialisés et davantage de techniciens et de conducteurs d'installations automatisées, chargés de la maintenance et de la programmation des machines.
Qu’en est-il réellement ? Le travail industriel n’est-il donc plus pénible ? Si la réalité du travail dans l'industrie n’est plus tout à fait celle des Temps modernes de Charlie Chaplin, ou de L’Établi de Robert Linhart, cela ne veut pas dire pour autant que les conditions de travail se sont améliorées. Au contraire, on peut affirmer que celles-ci se dégradent sous l’effet conjugué de trois phénomènes : les menaces de délocalisation et le chantage à l’emploi, l’introduction de méthodes de travail inspirées de la lean production, et les nouvelles technologies digitales.
Le déclin de l’industrie automobile française
Rappelons au préalable l’état de l’industrie automobile dans le pays. Celle-ci continue de jouer un rôle important dans l’économie nationale : avant la crise sanitaire, le secteur représentait 50 milliards d’euros d'exportation et générait 21,4 milliards d’euros de valeur ajoutée (Fogelman et Didioui, 2022). Cependant, elle connaît un déclin prononcé en matière de production et d’emplois depuis au moins quinze années en raison d’une « restructuration permanente » (Fayolle, 2005 ; Lomba, 2018), c’est-à-dire une succession de plans de licenciements, de délocalisations et de restructurations. Sa dimension permanente se retrouve notamment dans le fait que la restructuration devient un acte récurrent et ordinaire dans la vie de l’entreprise, sans nécessairement répondre à une situation de crise. Toutefois, en raison du poids économique du secteur automobile en France et malgré les efforts des directions, les suppressions d'emplois dans le secteur sont souvent peu discrètes. Ainsi, les quelques fermetures d’usines de constructeurs ou d’équipementiers ces dernières années ont donné lieu à des conflits collectifs médiatisés et suivis de près par les politiques (PSA Aulnay en 2013, PSA Sain-Ouen en 2018 et Renault Choisy-le-Roi en 2022, pour les constructeurs, GM&S en 2017, et SAM en 2021 pour les fournisseurs).
La désindustrialisation du secteur automobile se manifeste dans deux phénomènes : une baisse des volumes de production et une diminution continue de la main-d’œuvre. Ce phénomène ne date ni du Covid-19, ni même de la crise économique de 2008, mais d’avant, et correspond donc à une stratégie de long terme de la part des entreprises automobiles. La production de véhicules est en baisse constante depuis 2004, passant de 3,3 millions par an à 1,7 million en 2009, puis remontant à 1,9 million en 2019.
Cette baisse des volumes de production suit de près la baisse du nombre de salariés (graphique 1). En effet, entre 2004 et 2020, le secteur automobile français a perdu environ 130 000 emplois, soit 40 % de ses effectifs, et emploie aujourd’hui autour de 175 000 salariés. Cette baisse est principalement due au fait que le secteur automobile est un secteur à forte intensité de main d’œuvre, principalement dans les opérations d’assemblage, ce qui signifie qu’une baisse des volumes entraîne automatiquement une baisse de la main d'œuvre.
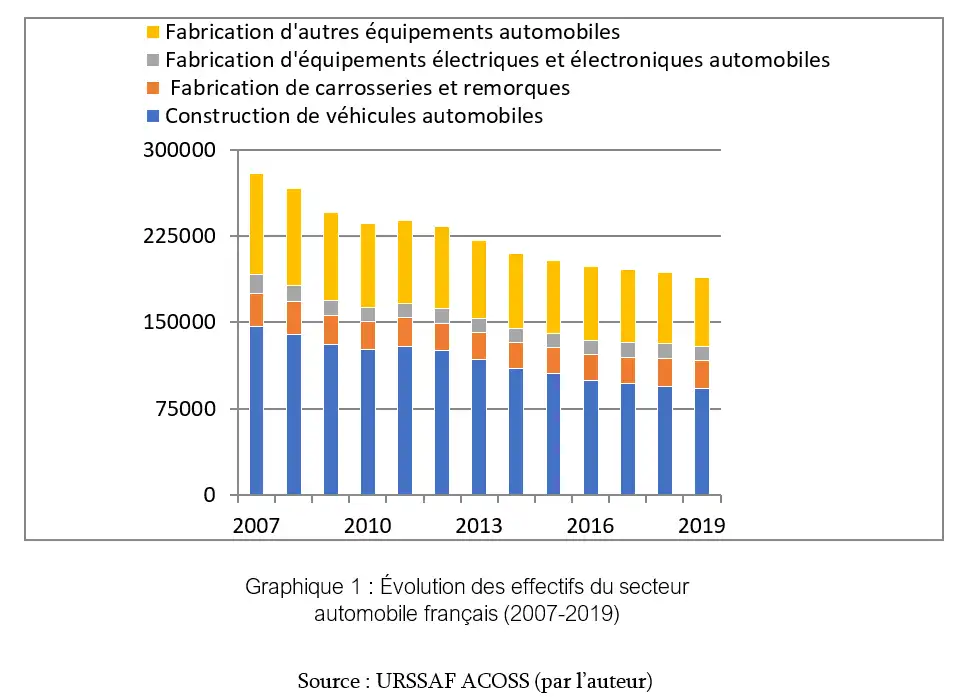
Qu’est-ce qui explique ce déclin du volume de production ? Il faut trouver la réponse dans la concurrence organisée par les constructeurs français avec les pays dits « à bas coûts », notamment sur le segment du bas de gamme et du low cost. La première vague de délocalisations a eu lieu dans les années 1990 et 2000 afin de conquérir les marchés émergents. La production des constructeurs automobiles français s’est déplacée de la France et de l’Europe de l’Ouest vers l’Europe de l’Est et la Turquie dans un premier temps, puis plus récemment vers l’Afrique du Nord (Pavlínek, 2020). Ces évolutions ont conduit à une structuration de l’industrie par zones régionales, avec une forte spécialisation entre pays, les petits modèles à fort volume étant assemblés dans la périphérie, et les modèles haut de gamme en Europe de l’Ouest. Par exemple, la production de véhicules à succès et à fort volume, comme la Dacia Logan, a été transférée en Roumanie (Pardi, 2018)
Ce déclin de l’industrie automobile française, et le transfert d’une partie importante de la production aux pays de la périphérie de l’Europe, est un premier facteur qui explique la dégradation des conditions de travail dans le secteur. En effet, comme nous verrons dans les parties suivantes, le chantage au maintien de l’emploi en France est devenu un puissant levier entre les mains des constructeurs lorsqu’il s’agit de revoir à la baisse les conditions de travail. Les entreprises automobiles sont engagées dans une course vers l'abîme (race to the bottom), qui emporte derrière elle les travailleurs des pays centraux et les travailleurs des périphéries intégrées. En même temps, la restructuration des usines en Europe de l’Ouest s’est accompagnée de nouveaux impératifs financiers de performance, ce qui s’est traduit par une révolution dans l’organisation du travail, avec l’introduction progressive de méthodes de travail venues du Japon, et du constructeur Toyota en particulier.
Au cœur de la dégradation des conditions de travail : la lean production
À partir du milieu des années 1970, les constructeurs d’automobiles en Europe et aux États-Unis font face à des marchés en crise. On voit alors se multiplier des plans de licenciement et des fermetures d’usines. Pourtant, au même moment, les constructeurs japonais sont en pleine croissance et les véhicules japonais commencent à envahir les marchés européens. Une véritable frénésie s’empare alors des industriels français, qui voient dans le « toyotisme », appelé plus tard lean production, une solution miracle aux problèmes de croissance de productivité dans l’industrie automobile française (Pardi, 2021).
Dans sa forme idéale, inspirée de son application au Japon, le lean promet des usines plus flexibles et plus résistantes aux crises en ne produisant que ce que le marché demande et en supprimant les stocks intermédiaires et le gaspillage. Du côté de la main-d’œuvre, celle-ci serait impliquée dans l’amélioration de la production, ce qui ferait que le travail deviendrait plus satisfaisant et les travailleurs plus autonomes et responsables. Cela prend la forme d’un système de suggestions (kaïzen), de « cercles de qualité » afin de traiter de différents problèmes (qualité, prix de revient, sécurité, etc.), ou du travail en équipes semi-autonomes de quelques dizaines de salariés (Shimizu, 1999).
Cependant, quarante ans après l’introduction du lean dans l’industrie automobile, on ne peut que constater ses effets néfastes pour les conditions de travail dans le monde et en France tout particulièrement. Dans les systèmes lean, deux facteurs sont sources de flexibilité de la production. Premièrement, l’overtime – un temps de travail ajouté d’habitude en fin de poste afin de rattraper des pertes de production – et les journées de travail supplémentaires et, deuxièmement, une main-d’œuvre intérimaire. Ainsi, la lean production est devenue dans l’industrie automobile mondiale synonyme de longues journées de travail, de travail les samedis et les dimanches, et de travail précaire. Par exemple, lorsque Toyota s’installe dans le Nord de la France et monte en cadence la production de la Yaris en 2004, un ouvrier sur quatre est intérimaire ou en CDD (Pardi, 2009). De la même façon, de l’overtime est utilisé afin de rattraper les pertes de production liées à des pannes ou des ruptures d’approvisionnement, mais il est aussi systématiquement utilisé afin de dépasser les programmes de production, dans la mesure où les pertes sont déjà intégrées dans les prévisions de production des usines. Par exemple, à l’usine PSA de Mulhouse, au mois de juin 2014, la ligne de montage qui fabrique les voitures Peugeot a perdu 85 unités, mais a « rattrapé » 247 véhicules grâce à l’overtime (Carbonell, 2020a). La durée de ces allongements horaires varie selon l’entreprise, elle est de 10 minutes chez Stellantis (mais de 40 minutes pour les équipes de nuit) et peut aller jusqu’à une heure chez Toyota.
Si la réduction des stocks est un des buts du lean c’est parce que derrière le stock il y a ce qui est conçu comme un « sur-effectif », l’excès d’hommes employés par rapport au niveau de la demande journalière ou hebdomadaire. En chassant les stocks, on chasse alors le sur-effectif et le sur-équipement. On cherche à atteindre l’« usine minumum », où l’usine est réduite à ses fonctions fondamentales : les équipements et les effectifs strictement requis pour satisfaire la demande journalière ou hebdomadaire. S’agit-il pour autant d’un système plus efficient ? Rien n’est moins sûr, dans la mesure où la réduction systématique du gaspillage et des pertes n’en fait pas un système plus flexible, mais au contraire rigide et fragile. Ce système, où les ressources ont été réduites au minimum nécessaire pour atteindre les objectifs journaliers, dépend de la stabilité du flux de production et de la faible variabilité des calendriers de production. Pardi (2021) rappelle que dès que ces deux facteurs ne sont pas au rendez-vous (comme avec le Covid-19 ou la guerre en Ukraine), la production et sa qualité sont compromises.
La pression sur les ouvriers n’a pas lieu qu’au niveau de l’organisation du travail, mais aussi dans les relations avec l’encadrement : le lean a souvent été décrit comme un « management par le stress » (Parker et Slaughter, 1990). Alors que la responsabilisation des équipes est présentée comme la source d’un travail plus intéressant, elle devient un outil de contrôle et de discipline. Par exemple, l’auto-contrôle des ouvriers est apparu comme un instrument majeur de responsabilisation des ouvriers, destiné à résoudre à peu de frais la question de la gestion du flux de pièces, de problèmes de qualité, et des défauts. Cependant, cette responsabilisation qui cherche à établir une relation de cause à effet entre l’ouvrier et ses actes a aussi une dimension morale. C’est-à-dire qu’elle se traduit bien souvent en une surveillance entre les ouvriers et en une dynamique accusatoire (Rot, 1998).
En effet, dès que la responsabilité de l’opérateur est établie, surtout lorsqu’il y a trop de défauts, l’opérateur risque d’être triplement sanctionné : symboliquement (il est convoqué par son chef), financièrement (il perd sa prime) et juridiquement (il peut être licencié). De la même façon, le travail en équipe s’est généralisé dans l’industrie automobile. Avec la promesse de gains de productivité, la main-d’œuvre a été divisée en groupes de 5 ou 20. Il ne s’agit pas là d’un changement technologique majeur, mais d’une réorganisation des relations de travail. Cependant, elle a eu des effets profonds sur les conditions de travail car derrière le travail en équipe se profile la concurrence entre les travailleurs (Parker et Slaughter, 1990). Si un ouvrier n’atteint pas les objectifs de qualité, c’est la prime collective qui n’est plus attribuée à l'équipe. Au lieu que ce soit l’organisation du travail qui soit pointée du doigt, ce sont les travailleurs absents, des handicaps, ou ceux qui ont du mal à suivre la cadence qui le sont (on retrouve ici l’« épistémologie du comportement » analysée par Philippe Askénazy et Damien Cartron dans leur contribution).
Enfin, le management par le stress ne s’exerce pas seulement sur les travailleurs pris individuellement, mais sur la main-d’œuvre dans son ensemble. La pression est mise sur la performance de chaque salarié, mais elle pèse aussi sur l’ensemble de l’usine qui se doit d’être « compétitive » au risque de fermer et que sa production soit délocalisée à l’étranger dans des pays à bas coûts, ce qui pousse les travailleurs à s’impliquer davantage dans leur travail.
Quand le lean et le chantage à l’emploi vont main dans la main
La restructuration de l’industrie automobile est donc allée de pair avec l’introduction de nouvelles méthodes de travail inspirées du « toyotisme ». La crise économique de 2008 a en outre favorisé l’approfondissement des logiques décrites plus haut à travers la négociation collective d’accords dits « de compétitivité » qui flexibilisent le temps de travail dans les établissements industriels, en échange d’un maintien de l’emploi industriel en France.
Ces accords qui ont vu le jour en 2012 ont été institutionnalisés dans l’Accord national interprofessionnel de janvier 2013 sous la forme d’« accords de maintien de l’emploi ». Ils sont ensuite devenus des « accords de préservation ou de développement de l’emploi » suite à la loi El Khomri de 2016. Puis les ordonnances Macron de septembre 2017 les ont remplacés par les « accords de performance collective » en modifiant le contexte et en diversifiant les objets de négociation. Dans les versions précédentes ces accords pouvaient être négociés dans un cadre strict défini par la loi, notamment seulement si les entreprises traversaient des difficultés économiques. De plus, ils devaient être négociés en échange de contreparties détaillées dans le préambule de l’accord. Mais au fur et à mesure des modifications du droit du travail, ces différentes contraintes ont été levées.
L’industrie automobile s’est saisi très tôt des possibilités offertes par les accords de compétitivité afin de négocier à la baisse les conditions de travail dans les usines. Dès juillet 2012, Sevelnord, une joint venture entre Fiat et PSA signe un accord collectif dont le but est de garantir le maintien des emplois en France, en échange d’un gel partiel des salaires et d’une plus grande flexibilité du temps de travail, avec, entre autres, l’introduction d’un overtime de 21 minutes par tournée. En juillet 2013, Française de Mécanique, une joint venture entre PSA et Renault qui fabrique des moteurs, lui emboîte le pas en négociant un accord collectif dont le but est de répondre à un « environnement en crise » devenue « structurelle ». Cette fois-ci encore, le maintien des emplois en France est accordé en échange d’un gel des salaires entre 2014 et 2015 et d’un temps de travail plus flexible. L’overtime y est également introduit : il peut durer entre 30 et 60 minutes par équipe. S’il est annoncé le jour même, il peut durer jusqu’à 30 minutes, si l’annonce a lieu la veille, le dispositif peut durer jusqu’à une heure.
Enfin, quelques mois après, c’est le tour de PSA et de Renault, de négocier des accords qui flexibilisent le temps de travail. Chez les deux constructeurs, les accords sont négociés tous les trois ans, ce qui permet de modifier en permanence les conditions de travail des salariés. À chaque occasion, l’entreprise s’engage sur des volumes de production et de ne pas délocaliser l’activité à l’étranger, en échange d’une plus grande flexibilité du temps de travail, entre autres choses. Outre l’overtime, PSA et Renault introduisent la modulation du temps de travail, mécanisme qui permet de faire varier à la hausse ou à la baisse le temps de travail sur la semaine et le mois, afin de répondre aux variations de la demande, aux pannes et aux ruptures d'approvisionnement. Par exemple, l’accord de 2013 chez PSA fait que les ouvriers qui travaillent en 2x8 le font désormais du lundi au samedi une semaine sur deux, en tournée du matin. Ensuite, lorsqu’il y a des pertes de production ou du chômage technique, les ouvriers doivent rattraper ces jours sous la forme de samedis supplémentaires non majorés, appelés « samedis gratuits » par les syndicats.
Ainsi, en dix ans, les « accords de compétitivité » sont devenus un outil essentiel de modification des conditions de travail dans l’industrie automobile, favorisant un approfondissement des logiques lean décrites plus haut (flexibilité du temps de travail, réactivité des installations, réduction des moyens). Comment comprendre ces transformations ? Le but des constructeurs est de réduire le stock de véhicules au minimum, de faire face à l’incertitude des marchés et de garantir la production journalière de véhicules. Ces contraintes se répercutent sur l’organisation du travail et donc sur la force de travail, avec davantage de flexibilité, avec des journées à rallonge, des semaines de six jours, et des horaires imprévisibles.
Cette stratégie n’est pourtant pas celle de tous les constructeurs en Europe, elle est propre à la France. À titre de comparaison, l’Allemagne a décidé de centrer sa production sur les produits haut de gamme, dont la fabrication nécessite plus de qualifications et de compétences. Quant à l’emploi automobile en Allemagne, il ne décline pas, mais se maintient. L’industrie automobile française rejoint donc autres les entreprises hexagonales visant une « stratégie low cost » décrite par Bruno Palier dans sa contribution, faite de délocalisations, de sous-traitance, de bas salaires, et de mauvaises conditions de travail.
L’essor du numérique dans l’industrie : enfin un travail moins pénible ?
Au même moment que se multipliaient les accords de compétitivité, on a vu resurgir les promesses d’un travail moins pénible grâce au développement de ce qu’on désigne par Industrie 4.0 ou par digital manufacturing. Ce phénomène correspond à l’utilisation de données numériques dans l’optimisation des procès de travail et dans l’amélioration des produits. Plus précisément, il renvoie à l’établissement de réseaux cyber-physiques de machines interconnectées, à l’analyse et le contrôle du processus de travail par l’échange d'informations en temps réel. Les discours mainstream sur l’Industrie 4.0 décrivent ces technologies comme un moyen d’améliorer les conditions de travail. Comme pour le lean, ils promettent plus d’autonomie aux salariés et un travail plus intéressant. De nouvelles formations et qualifications deviendraient nécessaires au fur et à mesure que l’informatique pénètre les procédés industriels et que le travail devient plus complexe et abstrait (Kohler et Weisz, 2016).
Ce n’est pourtant pas la première fois que le changement technologique est brandi comme un moyen de rendre le travail moins pénible. Dès les années 1980, plusieurs constructeurs font la tentative d’automatiser une partie de l’assemblage et d’éliminer les postes 3-D (difficult, dangerous and dirty). Cependant, cette stratégie high-tech d’investissements coûteux est abandonnée au profit d'une stratégie low cost qui repose davantage sur la flexibilité offerte par le lean. Ce dernier semblait un moyen plus approprié afin d’ajuster la production à la demande et d’améliorer la qualité des produits. En fin de compte, des usines trop automatisées étaient trop « lourdes » et souffraient de trop de pannes et d’erreurs dans le produit final (Fujimoto, 1997).
À différence de l’automatisation, le digital manufacturing n’est pas contradictoire avec le lean, mais peut agir même comme une extension de celui-ci (Moro et Virgillito, 2022). En effet, les outils connectés permettent une saturation des rythmes de travail et une concentration des ouvriers dans les gestes à valeur ajoutée. C’est le cas avec l’introduction du kiting et du pick-to-light ou du pick-to-voice dans l’approvisionnement de pièces sur les postes de montage, organisation du travail qui s’est généralisée dans les usines d’assemblage ces dernières années.
En amont de la chaîne, des ouvriers sélectionnent des pièces à partir de voyants qui s’allument, ou à partir d’une voix qui dicte les consignes dans un casque. Le but est de réduire les erreurs et de réduire le temps de saisie des pièces. Des kits avec les pièces sont ensuite assemblés et livrés par des robots appelés automated guided vehicles, ou AGV, sur les postes de montage, où des monteurs placent les pièces sur les véhicules. Les ouvriers monteurs n'ont plus besoin de se déplacer autour du véhicule pour s'approvisionner en pièces, ils ne commettent plus d’erreurs en assemblant les mauvaises pièces et n’ont plus à porter des pièces lourdes. Cependant, leur rythme de travail s’accélère, dans la mesure où des temps morts sont supprimés et dans la mesure où il dépend désormais de la livraison de pièces par les AGV (Carbonell, 2020b).
On peut voir que ce système n’augmente pas l’autonomie ou la responsabilité des ouvriers, ni rend le travail plus intéressant. Au contraire, dans ce système, les salariés perdent en autonomie et se laissent guider par les technologies, au lieu d’être activement impliqués dans le déroulement du travail (Butollo Jürgens et Krzywdzinski, 2019). Ce qui rejoint la contribution de Christine Erhel, Mathilde Guergoat Larivière et Malo Mofakhami, qui rappelle que le changement technologique, loin de libérer les individus des tâches pénibles, intensifie le travail, et ce d’autant plus chez les employés et les ouvriers.
Si le travail à la chaîne ne ressemble plus à celui des années 1970, les conditions de travail ne se sont pas pour autant améliorées. L’introduction du lean, vu comme une réponse aux problèmes de motivation de la main-d’oeuvre et à la baisse de la productivité, couplée à la digitalisation de la production, n’ont pas redonné du sens au travail (voir la contribution de Coralie Perez et Thomas Coutrot), mais au contraire ont contribué à l’émergence de nouvelles formes de subordination au travail. En même temps, le contexte de crise et de restructuration permanente favorise un chantage à l'emploi qui autorise aux constructeurs de demander des sacrifices aux salariés, sans pour autant que la tendance à la désindustrialisation se soit inversée.
Bibliographie
- Butollo Florian, Jürgens Ulrich, Krzywdzinski Martin, « From Lean Production to Industrie 4.0: More Autonomy for Employees? », dans Uli Meyer, Simon Schaupp et David Seibt (eds) Digitalization in Industry. Between Domination and Emancipation, Palgrave Macmillan, 2019, p. 61-80.
- Carbonell Juan Sebastian, « L’éclatement du cadre temporel fordien dans l’industrie automobile », Temporalités [En ligne], 31-32, 2020a, mis en ligne le 03 février 2021, consulté le 07 juin 2023.
- Carbonell Juan Sebastian, « The Factory of the Future? The Contradictory Restructuring of an Assembly Line in France », Sociologia del lavoro, 158 (3), p. 118-136, 2020b.
- Fayolle Jacky, « Restructurations d'hier et d'aujourd'hui : Les apports d'un séminaire », La Revue de l'Ires, 47 (1), p. 337-362, 2005.
- Fogelman Myriam et Didioui Amine, « Transformations et défis de la filière automobile », Les Thémas de la DGE, n° 4, octobre 2022.
- Fujimoto Takahiro, « Strategies for Assembly Automation in the Automobile Industry », dans Koichi Shimokawa, Ulrich Jürgens and Takahiro Fujimoto (eds.), Transforming Automobile Assembly, Springer, Berlin, 1997, p. 211-237.
- Kohler Dorothée et Weisz Jean-Daniel, Industrie 4.0. Les défis de la transformation numérique du modèle industriel allemand, Paris, La Documentation française, 2016.
- Lomba Cédric, La restructuration permanente de la condition ouvrière. De Cockerill à ArcelorMittal, Vulaines-sur-Seine, Éditions du Croquant, 2018.
- Moro Angelo et Virgillito Maria Enrica, « Towards Factory 4.0? Convergence and divergence of lean models in Italian automotive plants », International Journal of Automotive Technology and Management, 22 (2), p. 245-271, 2022.
- Parker Mike et Slaughter Jane, « Management‐by‐stress: The team concept in the US auto industry », Science as Culture, 1 (8), 27-58, 1990.
- Pardi Tommaso, « Travailler chez Toyota : de l'emploi à vie à la course à la survie », La Revue de l'Ires, 62, p. 39-70, 2009.
- Pardi Tommaso,, « Une voiture low cost pour les pays riches », La nouvelle revue du travail [En ligne], 12, 2018, mis en ligne le 01 mai 2018, consulté le 07 juin 2023. URL : http://journals.openedition.org/nrt/3544 ; DOI : https://doi.org/10.4000/nrt.3544
- Pardi Tommaso, « Lean Production in the Automotive Industry: Origin, Diffusion, Paradoxes, and Contradictions of a New Managerial Paradigm », dans Thomas Janoski et Darina Lepadatu (Eds.), The Cambridge International Handbook of Lean Production: Diverging Theories and New Industries around the World, Cambridge University Press, 2021, p. 204-226.
- Pavlínek Petr, « Restructuring and internationalization of the European automotive industry », Journal of Economic Geography, 20 (2), p. 09-54, 2020.
- Rot Gwenaële, « Autocontrôle, traçabilité, responsabilité », Sociologie du travail, 40 (1), p. 5-20, 1998.
- Shimizu Koïchi, Le Toyotisme, Paris, La Découverte, 1999.